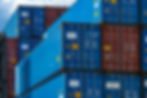
The global supply chain is becoming increasingly complicated for U.S. shippers, especially with new revelations surrounding transshipment schemes and the growing enforcement of tariffs on Chinese-made goods. For shippers handling imports, it’s essential to stay ahead of the curve when it comes to regulations, as recent investigations into the kitchen cabinet industry have revealed alarming risks that can directly impact business operations and costs.
In late 2022, U.S. Customs and Border Protection (CBP) agents were called to investigate a Malaysian factory linked to Qingdao Haiyan Group, a major supplier in the U.S. cabinet market. The investigation uncovered a complex transshipment scheme where Chinese-made cabinets were sent to Malaysia and relabeled as Malaysian products, thus evading the U.S. tariffs on Chinese goods. This process is not unique to the cabinet industry but has been observed in other sectors like mattresses, solar panels, and quartz countertops. As transshipment schemes become more sophisticated, U.S. companies and shippers must ensure compliance to avoid hefty fines, delayed shipments, and strained relationships with customers.

Transshipment: The Hidden Risk in the Supply Chain
Transshipment is the practice of rerouting goods through a third country to obscure the original country of manufacture. In this case, Haiyan allegedly shipped Chinese-made cabinets through Malaysia, masking their true origin to avoid tariffs. This isn't an isolated issue. U.S. Customs has already prevented over $500 million in duty evasion through similar investigations across various industries.
The problem arises from the temptation to circumvent tariffs—imposed under both the Trump and Biden administrations—to make products cheaper for U.S. consumers. However, as Customs and Border Protection tightens regulations, companies caught in transshipment schemes face penalties, loss of reputation, and a breakdown in supply chain trust.
For shippers, the key takeaway is clear: ensuring compliance with both U.S. import regulations and international trade laws is critical to safeguarding operations. The risks of missing key compliance checks or being unaware of the transshipment practices of a supplier can result in severe financial penalties, including additional tariffs and shipping delays.
U.S. Cabinet Industry: A Case Study in the Risks of Non-Compliance
The ongoing investigation into Qingdao Haiyan Group highlights these challenges. Despite being a significant supplier to major U.S. retailers like Lowe’s and Home Depot, Haiyan's operations were questioned after evidence showed that its Malaysian subsidiary was improperly relabeling Chinese products. As a result, the Kitchen Cabinet Manufacturers Association (KCMA) brought a complaint to CBP, urging the agency to enforce stricter import controls.
Companies like Cabinets To Go, who were affected by this transshipping scheme, have felt the financial burden. After receiving cabinets labeled as “Made in Malaysia,” they discovered that the goods had actually been sourced from China, leading to over $650,000 in additional tariff costs. This situation highlights the need for U.S. shippers to carefully vet their suppliers and ensure that all imported goods are correctly labeled and accounted for.
What Can U.S. Shippers Do to Avoid Transshipment and Tariff Pitfalls?
To avoid falling victim to transshipment schemes and the penalties associated with tariff evasion, here are a few key steps U.S. shippers can take:
Work with Trusted Suppliers: Choose suppliers that have a proven track record of transparency and compliance with U.S. trade regulations. Ensure they provide accurate and verifiable documentation about the origin of their goods.
Conduct Regular Audits: It’s essential to regularly audit your suppliers and shipments to verify that the products being imported match their country of origin. Implement a thorough inspection process to catch discrepancies before shipments reach U.S. ports.
Stay Updated on Tariff and Trade Policies: U.S. trade policies are constantly evolving. Whether it’s tariffs, antidumping duties, or new import regulations, shippers must stay informed. Working with a reliable consulting firm can help ensure your supply chain is always compliant with the latest changes.
Leverage Technology: Implementing technology solutions that track and document the origin of goods can help prevent mistakes or fraudulent practices in the supply chain. Customs declarations should be meticulously checked to ensure that they reflect the true origins of the products.
Collaborate with Legal and Trade Experts: Having an experienced legal and trade advisory team can help identify potential risks in your supply chain and offer guidance on best practices. These professionals can help you navigate the complexities of global trade and tariff regulations.
Conclusion
The recent investigations into transshipment in the kitchen cabinet industry serve as a wake-up call for all U.S. shippers. Whether you're in the cabinet business or another sector, staying vigilant about tariff evasion and ensuring the accuracy of your import declarations is more important than ever. By taking proactive steps to verify the legitimacy of your supply chain and working with trusted experts, you can protect your business from costly compliance errors and maintain smooth operations in an increasingly complex global marketplace.
At Gain Consulting, we specialize in helping businesses navigate the intricate world of global supply chains, ensuring compliance with U.S. import regulations and avoiding costly pitfalls like transshipment schemes. Contact us today to learn how we can support your business in maintaining a reliable and efficient supply chain.